Spray drift reduces coverage on the target
Spray drift is a risk to every application. It can stop you spraying, may damage off-targets and can reduce pesticide coverage on the target reducing performance.
Timely on-target spray application is a must for effective pesticide performance, but even on a good spray day wind gusts can cause drift.
Drift has implications for the environment, bystanders, and off-target crops. The products you are applying in your tank-mix, the conditions in which you apply your spray, and your spraying practices all have drift implications. Raising the spray boom from 40cm to 70cm increases the risk two-fold.
Users of plant protection products must ensure that all reasonable precautions are taken to prevent spray drift.
Potential impact of spray drift:
- Damage to off-targets
- Potential for MRL exceedance in non-target crops
- Can delay spraying
- Reduced deposition on the target
- Reduced coverage on the target
- Wastes expensive pesticides
What is spray drift?
Spray drift is the uncontrolled movement by wind, of any pesticide away from the targeted area.
The three main forms of drift are:
- Droplet drift
- Vapour drift
- Particulate drift
Droplet drift is the main cause of off-target damage.
Spray drift is the biggest cause of off-target chemical movement
It may damage non-target crops near by – Drift is a serious concern, especially when spraying herbicides next to a field with a different crop / cover crop. Even a small amount of drift can create significant crop damage, especially in sensitive speciality crops.
Potential for MRL exceedance – Spray drift from neighbouring fields can lead to MRL exceedances.
Can lead to poor performance due to under-dosing – Drift has big consequences for the target. It could result in a sub-lethal dose being applied.
Spray drift reduces coverage on the target – Drift may lead to insufficient coverage for the application to be effective.
Wastes expensive pesticides – Crop protection inputs are a big investment, not to mention the time and money spent applying them. Allowing them to drift away, is an expensive waste.
Can delay spraying – To hit crucial spray timings and ensure inputs work as effectively as possible, spray operators need to maximise their time spent in the field on good spraying days. But even on the perfect spray day, wind gusts can mean it’s just too risky, causing you to delay spraying. This has serious implications for crops such as potatoes, where maintaining blight spray intervals every 7 days is crucial to keep on top of blight.
A lot of factors can increase spray drift, reducing coverage on the target
The short distance from the spray nozzle to the target may only be 50cm, but there are a lot of factors that increase the risk of drift and compromise your spray reaching its intended destination.
1. Physical & chemical properties of the pesticide
Pesticide formulations vary in droplet size. Larger, heavier droplets will reach their target quicker due to gravity and are less likely to drift. Smaller, lighter droplets are more susceptible to the effects of drag – they will move slower and are more likely to be suspended in the air for longer, increasing the risk of drift. Spray droplets less than 100 microns are the most susceptible to drift.
2. Spraying practices used e.g. spray quality produced by the sprayer; distance between the nozzle and target; speed of travel
Spray quality is dependent on forward speed and nozzle choice. As forward speed is increased, application rate is reduced. Rate controllers on the sprayer, used to maintain application rates increase pressure which are more likely to cause spray drift. Nozzle choice also impacts spray quality and drift risk. The product label will advise the correct spray quality for the product you’re applying. A nozzle producing a fine / very fine spray quality will enhance the likelihood of drift.
Increasing forward speed increases turbulence, creating the conditions where drift may occur. Increasing forward speed will also impact boom height and stability.
Spray drift doubles when the spray boom is raised from 40cm to 70cm, and again from 70cm to 80cm.
3. Environmental conditions at spraying e.g. wind velocity and direction; relative humidity and temperature
Trials have shown that even on a perfect spray day, with an average wind speed of 1.2 metres/second, the actual wind speed can vary from 0.1 to 4.3 metres/second. Such gusts of wind, even within the width of the spray boom, have the potential to leave patches of crop underdosed.
At 25oC and above, especially with low humidity, unpredictable air currents can occur, creating the conditions for spray drift.
Pre-ems, post-emegence herbicides & late season sprays are most at risk
Pre-emergence applications – can be high risk for drift due to bare soils that release stored heat causing air/spray to rise, and there being no crop to intercept the spray.
Post-emergence herbicides – most herbicides are applied as a fine spray quality. The smaller droplets provide better coverage, which is important when the target surface is small, but the fine droplets are more prone to drift.
Late-season applications – Spraying later in the life of the crop can increase the risk of spray drift. This is because the taller crop increases the height of the boom and the potential for drift to occur.
Our top tips to minimise drift & improve coverage on the target
- Spray at low wind velocities – spraying when the wind speed is between 1.2 and 6 mph is the optimum window with ideal spraying conditions between 2 and 4 mph.
- Slow and steady forward speed – try to stick to 10-12 kph where possible.
- Maintain boom height at 50cm – the lower the boom, the lower the drift risk.
- Use the right nozzle at the right pressure – be aware that drift reducing nozzles can also reduce coverage as they create larger droplets.
- Use a drift retardant or an adjuvant such as Kantor with anti-drift properties to eliminate drift and maximise coverage.
Learn how Drift Retardants & Adjuvants can help

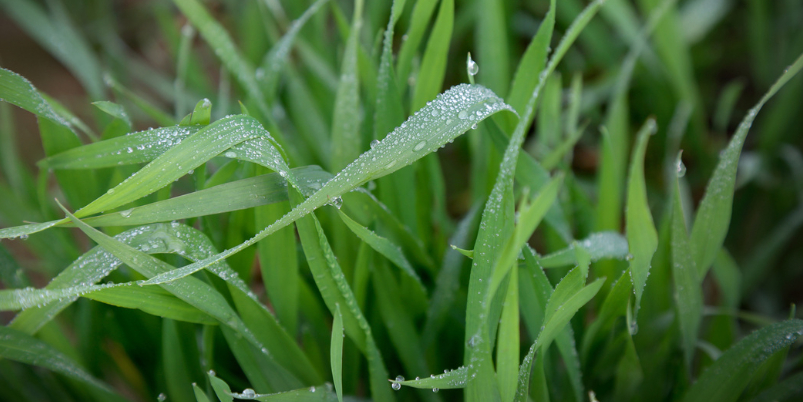
They’re not all muck and mystery! Master tank mix adjuvants and you’ll be able to select the right ones so you can push your pesticide performance to the max.
Learn more
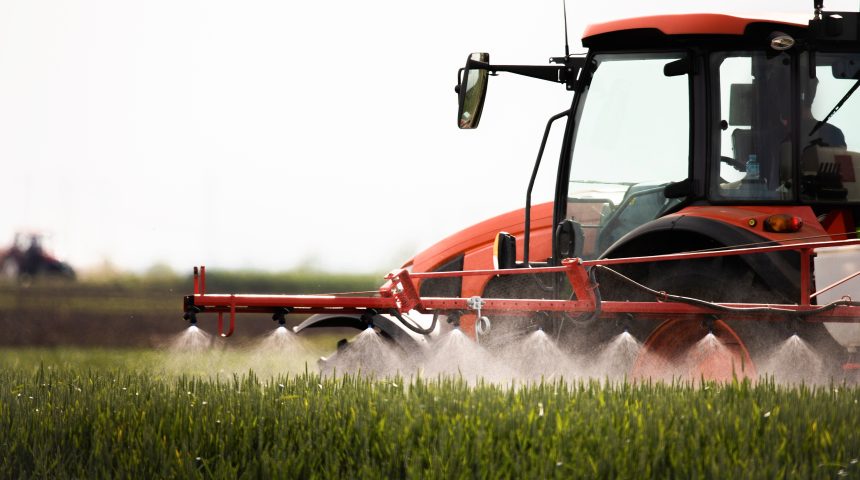
Timely on-target spray application is a key objective for effective pesticide applications, but even on a “good” spray day, drift may set you back. Adding a drift retardant in to the spray tank will help combat drift and keep your sprays on target.
Learn more